Geomaterials Products
Geomaterials Products
Production of GEOMATERIALS Foam Glass
Used glass as a raw material
GEOMATERIALS Foam Glass is a high quality insulation material made of 100% recovered glass. Recycled glass is crushed into extremely fine powder and blended with foaming agents. This process reuses valuable raw materials and saves energy initially required for the production of glass. Due to this, the energy used in producing GEOMATERIALS Foam Glass is significantly reduced.
The Manufacturing Process of GEOMATERIALS Foam Glass
GEOMATERIALS Foam Glass is sintered at high temperatures. Foam glass occurs out of glass powder during an expansion process in the latest conveyor ovens at a temperature of approximately 900°C. The foam glass cake comes out of the kiln on the conveyor belt to cool down. During this cooling process, tension cracks occur and so it breaks down into our foam glass gravel. This activity results in the GEOMATERIALS Foam Glass having a closed cell structure, which is evenly distributed.
The finished GEOMATERIALS Foam Glass stands for sustainability through recycling. This makes it particularly environmentally friendly.
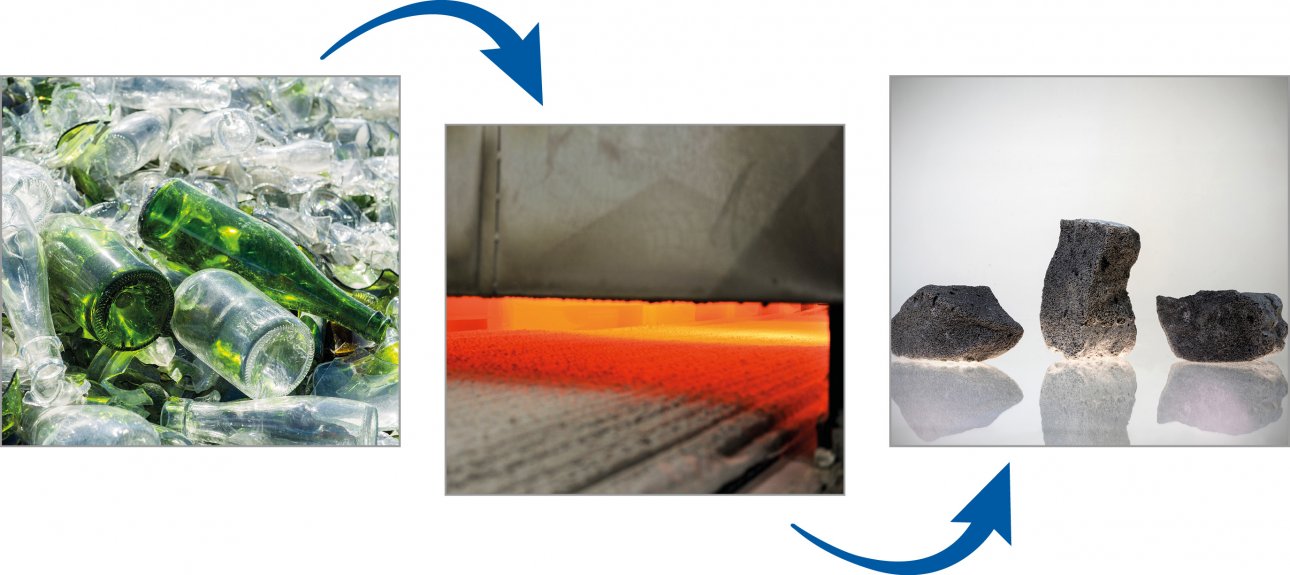
Area of Application
GEOMATERIALS Foam Glass
Installation guidance
The use of GEOMATERIALS Foam Glass in the capillary fringe of groundwater or water source areas is not allowed. The natural ground must be well permeable to water. In the presence of cohesive or stratified soils, where accumulation or stratum water can occur, a drainage according to DIN 4095 has to be provided.
-
Excavation
Excavate immediately prior to the introduction of GEOMATERIALS Foam Glass to meet flatness and compressive strength in accordance
with the object-related requirements. Unless otherwise specified, the requirements for flatness and compressive strength should be based on the
principles of ZTVE – StB 94. Lay sewage pipes in pipe trenches and fill with sand on sub-grade level.
-
Lay the GEOTEXTILE
Set up the formwork for GEOMATERIALS Foam Glass and lay out the flat surface with geo-textile (150g/m²) overlapping. Provide sufficient overhang so that the finished fill can be completely packed later. Position splice bars marking the compacted (final) height of GEOMATERIALS Foam Glass, at regular intervals.
-
Install GEOMATERIALS Foam Glass
If GEOMATERIALS Foam Glass is delivered loose, it is offloaded directly into the excavated pit. Above the installation site, the Big Bags have to be lifted and opened from below with the help of an excavator or crane.
-
Distribute GEOMATERIALS Foam Glass
At smaller sites, level GEOMATERIALS Foam Glass uniformly to the marked height using an excavator shovel and rakes. For larger construction sites a mechanical distribution is carried out before the head by a charger or a shovel. Driving over the uncompacted material should be avoided, as precompaction increases material consumption.
-
Compact GEOMATERIALS Foam Glass
For small sites, compacting shall be performed by a lightweight vibration plate (weight: 80-100 kg, frequency: 85-100 Hz, supporting area: 50 cm, straight running). For areas > 200 m² you can use a soil compactor. A compression exceeding the specifications, results in a higher material consumption, but does not have any negative impact on the technical properties. For design thickness greater than 30 cm, GEOMATERIALS Foam Glass must be dumped in two layers and each layer has to be compacted. The flatness of the surface has to be made before the compacting process, so that at least a flatness tolerance of +- 3 cm in relation to a length of 4 m is achieved.
-
Lay the separation layer
After completion of compression, the Geotextile is wrapped-up laterally and the entire GEOMATERIALS Foam Glass layer is covered with a PE-foil to protect against cement residue.
-
Install formwork for foundation slab
Place the formwork for the floor slab directly on the prepared surface and create the floor slab according to the specification. The ring drainage (sewer pipes) is laid around the pit after the formwork has been removed.
-
Closing remark
According to the General Building Inspectorate Approval, a PE film must be placed on the compacted surface of GEOMATERIALS Foam Glass, except for project-related, justified deviations. GEOMATERIALS Foam Glass walkable at a compression ratio of 1.3 to 1. From a compression ratio of 1.6 to 1, careful driving is possible (axle load up to 7.0t). The compacted planum must not be damaged.
-
Evenness of the subgrade
An evenness of the subgrade after compaction of +/-3cm over a measuring length of 4 m can be achieved with GEOMATERIALS Foam Glass.
Recommended equipment for installation of GEOMATERIALS Foam Glass
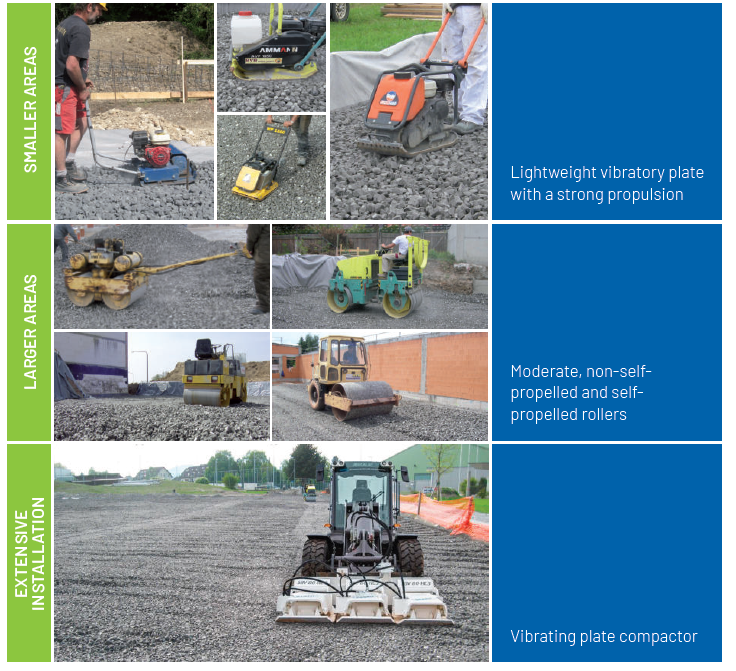
Possibilities for delivery
Delivery of bulk material with a walking floor truck
This form of delivery is suitable for construction sites, which can be easily reached. A walking floor truck cannot tilt, but rather shuffles the material with its moving floor from back to front.
Typical dimensions: LxWxH = 18 x 4 x 2,8 m
Loading capacity: 85 - 95 m³ depending on type of truck
Non steerable axles!
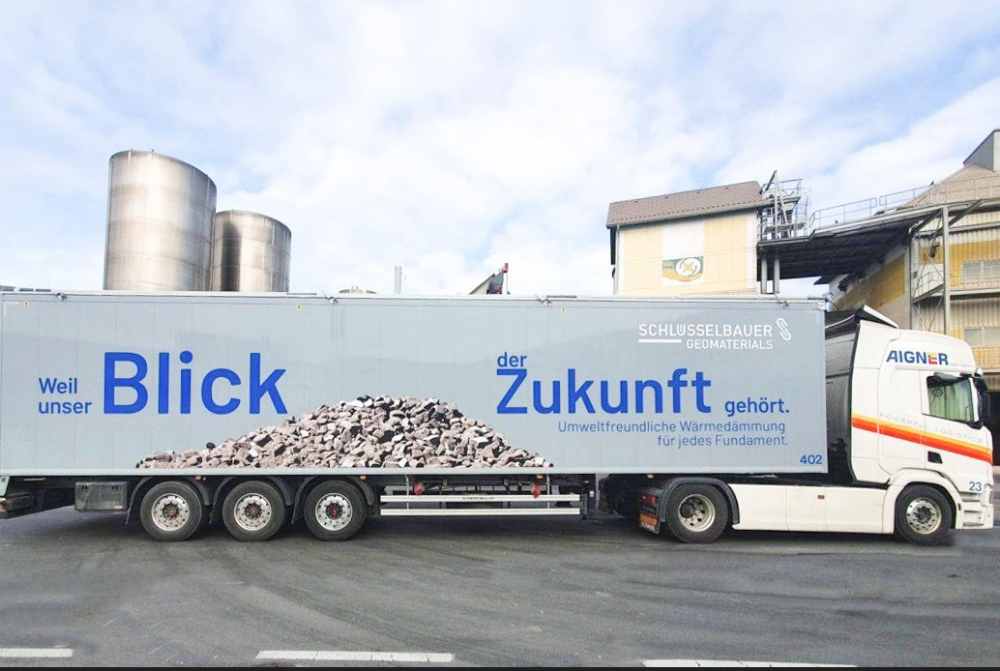
Delivery of bulk material with a container truck
This form of delivery is suitable for narrow access roads. The bulk material is divided into the towing vehicle and a
trailer. Therefore the material can be brought step by step. Please mind: through the minimized quantity and the additional expense, we charge an extra container surcharge.
Typical dimensions towing vehicle: LxWxH = 9 x 4 x 2,8 m
Loading capacity: 76 - 80 m³ depending on type of truck
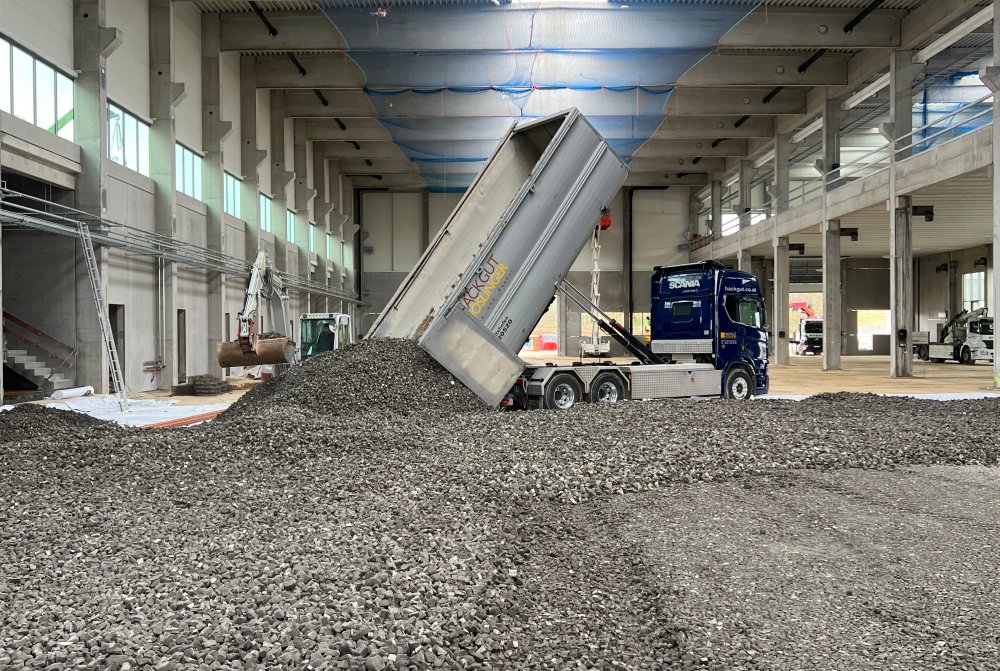
Delivery packed in Big Bags
We also offer the material in packaged form (disposable packaging):
GEOMATERIALS Schaumglas Big Bag 1,5 m³
GEOMATERIALS Schaumglas Big Bag 2 m³
GEOMATERIALS Schaumglas Big Bag 3 m³
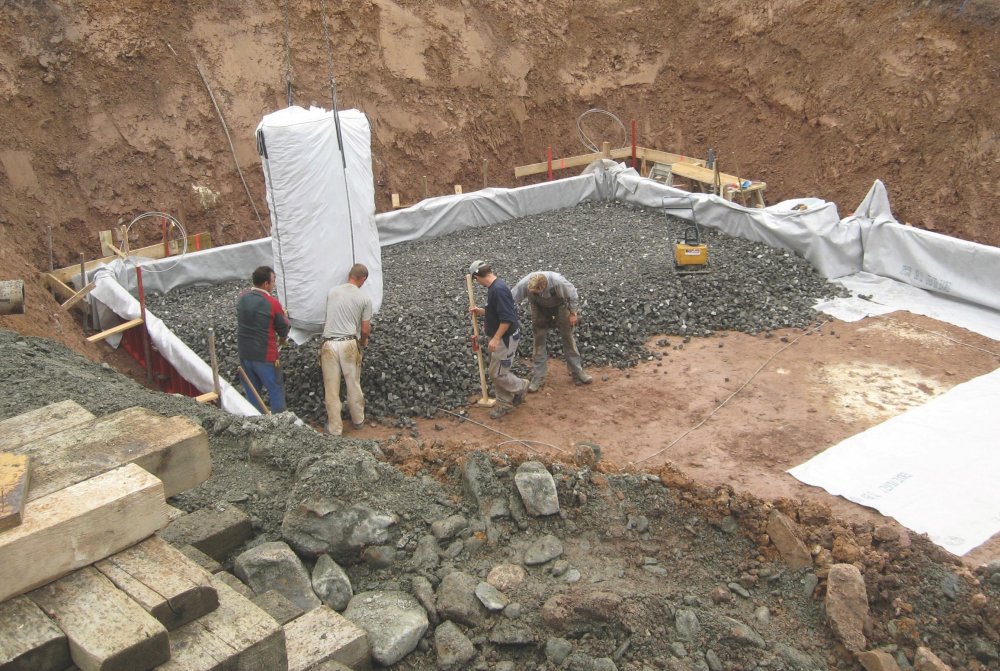
Installation with a dispensation-towel
Especially for stepped, impassable areas, there is the possibility to install the bulk material with the help of a dispensation-towel.
The material is conveyed from the walking floor truck into the towel, spread on the ground with a capacity of 12 m³. The dispensation-towel can be moved with a crane. The distribution of the material happens through the outlet spigot. We gladly provide the dispensation-towel for a daily fee.
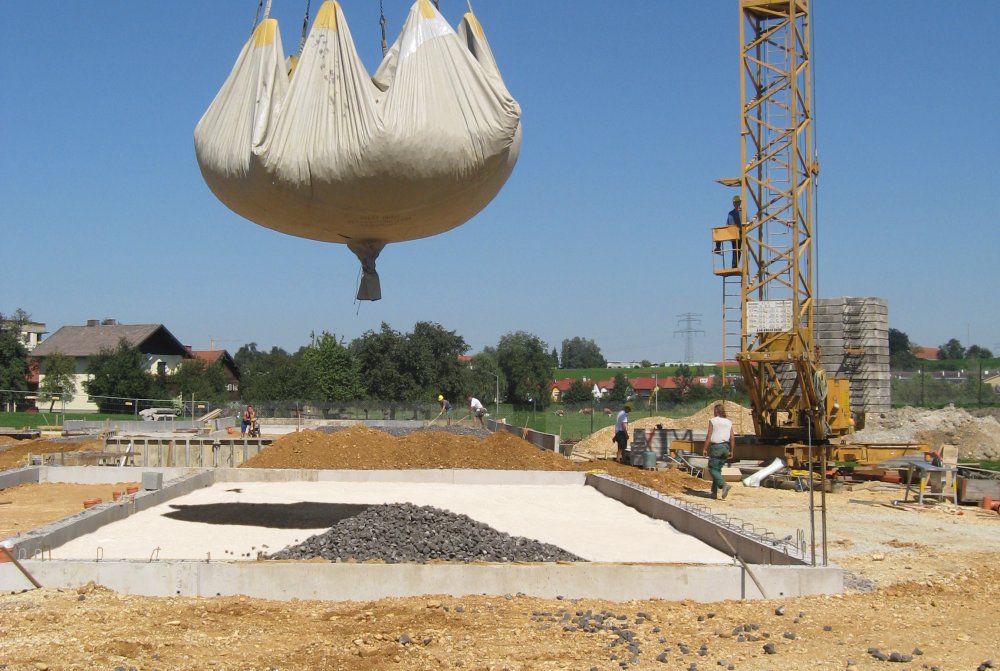